Creating an ideal listening environment in your home studio or music room requires effective sound dampening with acoustic foam panels.
The manufacturing process for acoustic foam involves precision molding, curing, testing and assembly using materials like polyurethane foam and melamine selected for optimal noise reduction.
Let’s dive into the key steps for constructing these sound-absorbing foam pieces.
How is Acoustic Foam Made?
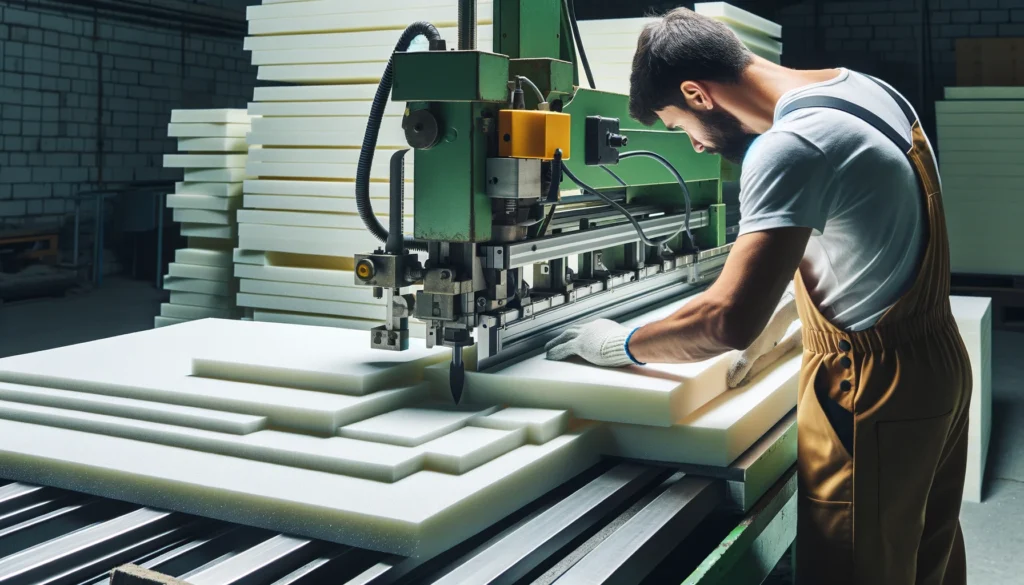
Acoustic foam is made by molding flexible sound-dampening materials like polyurethane into geometric forms optimized for absorbing audio frequencies.
Manufacturing processes include cutting, shaping, curing, testing and assembly to produce finished foam pieces and panels with precision acoustics.
Now let’s delve deeper into the foam production steps.
Raw Materials Used
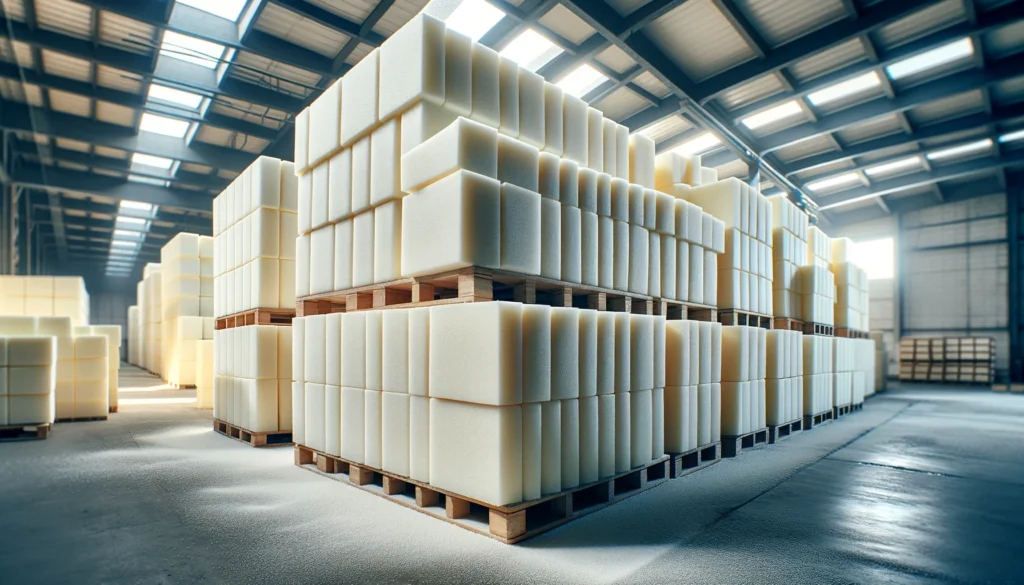
There are several raw materials that go into the creation of acoustic foam.
The base material is most commonly polyurethane foam.
Polyurethane is preferred for its acoustic properties, flexibility, cost-effectiveness, and ability to be molded into different shapes.
Fiberglass may also be used as a raw material in certain types of acoustic foam production.
Fiberglass allows the foam to be semi-rigid while still providing sound dampening.
Basalt rock wool, which consists of fine fibers drawn from natural volcanic basalt rock, is another option.
It is known for its high heat resistance.
Finally, melamine foam is occasionally utilized as a raw material as well.
Melamine foam is very porous, which enables exceptional sound absorption.
The specific raw materials used depend on the desired characteristics and end-use application of the acoustic foam.
By varying the materials, manufacturers can tweak the density, porosity, sound absorption coefficients, fire ratings, thermal resistance, cost, and other qualities.
Aside from various foam bases, other raw materials like dyes, pigments, adhesives, and protective coatings may be incorporated into the acoustic foam production process.
Shaping and Molding
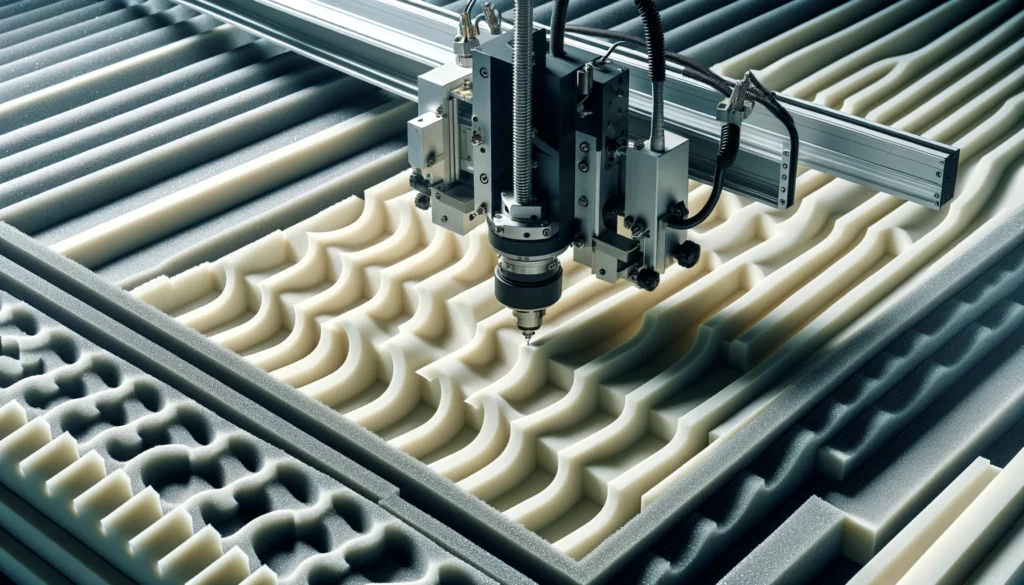
The raw foam material arrives at factories in large blocks.
It then needs to be shaped into the necessary geometric configurations required for optimal sound dampening.
Common shapes include wedges, pyramids, waves, eggshells, and custom contours.
The shaping begins by slicing the foam blocks to the specified thickness required using cutting machines or heated wires.
The slices are then compressed into molds in order to form the particular shapes needed.
The molds used are usually CNC machined to precise specifications and can create angles as small as 20 degrees for wedge shapes.
Custom molds are also designed for unique acoustic applications like studios or theaters.
The molded foam shapes are then cured using one of three methods: oven cured, chemically cured, or air cured.
Oven curing sets the shape rapidly using heat.
Chemical curing utilizes additional liquids that trigger hardening.
Air curing is done at room temperature over several days.
The curing process ensures the foam retains its molded structure.
Adding Color and Texture
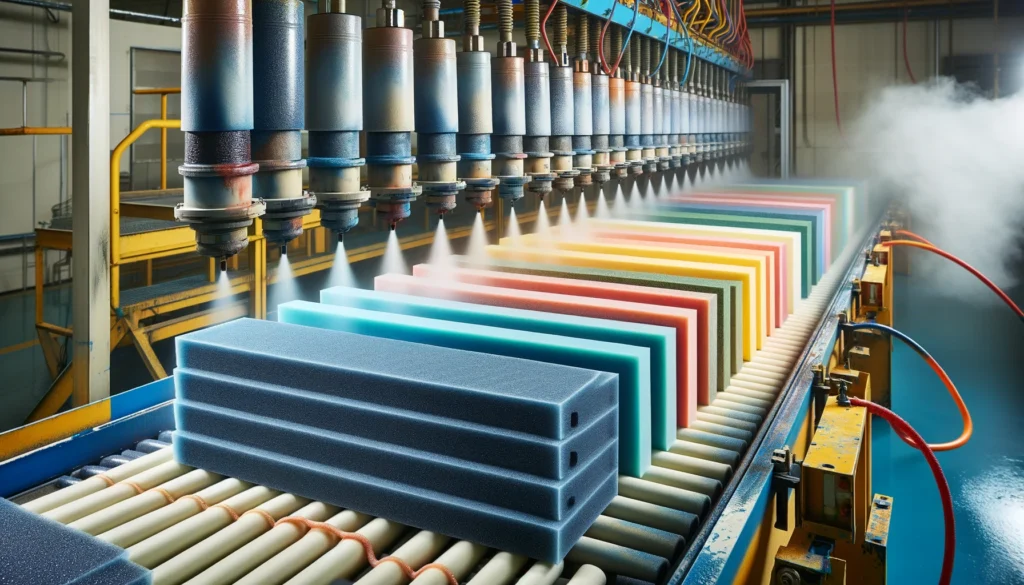
While acoustic foam typically starts as a neutral white or cream color, custom colors and finishes can be added as well.
This enhances visual appeal for interior design purposes.
The coloration is achieved by mixing dyes or pigments into the foam material during production.
Any color can be obtained, although lighter shades are most common as darker hues reduce acoustic performance slightly.
Aside from colors, different textures may also be applied to the visible surface of the finished acoustic foam pieces.
Small bumps can be embossed into the foam when compressed into the mold.
Some textures mimic suede or fabric looks.
Decorative finishes can also be adhered to the facing area while still preserving acoustic integrity on the inner foam.
Assembly and Gluing
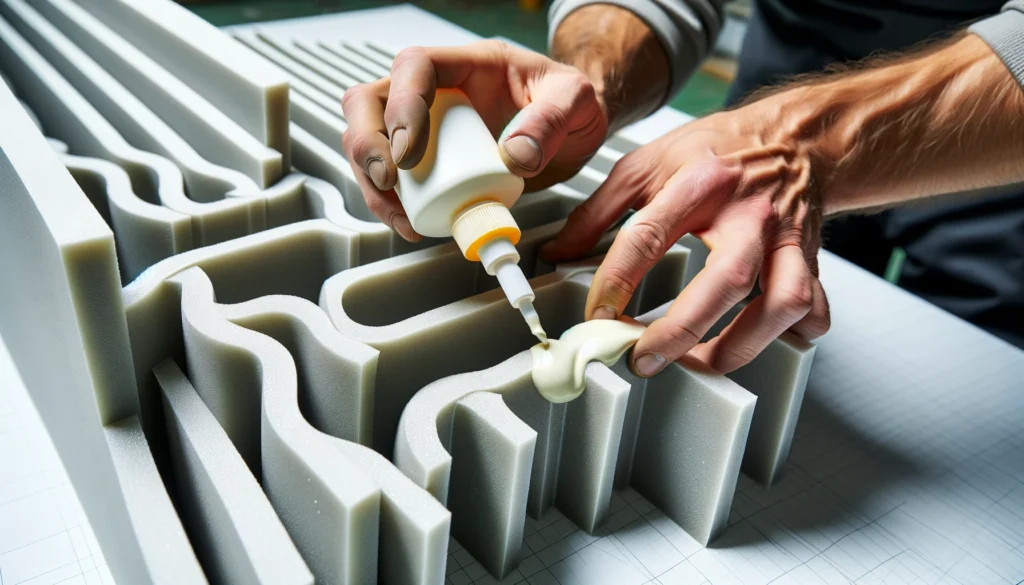
For more complex acoustic foam elements like 3D contours or intricate shapes, multiple pieces need to be assembled.This requires precise cutting and joining.To assemble, glue is applied to the edges of the foam pieces.
The pieces are then pressed together, held, and allowed time to cure.
The glues used for acoustic foam include acoustic-grade adhesives that deliver robust bonds while not hampering porosity or acoustic characteristics.
In addition to assembly, mounting hardware like pre-applied adhesive strips or hook and loop tape may be added to the backsides of foam panels during this stage as well.
Performance Testing
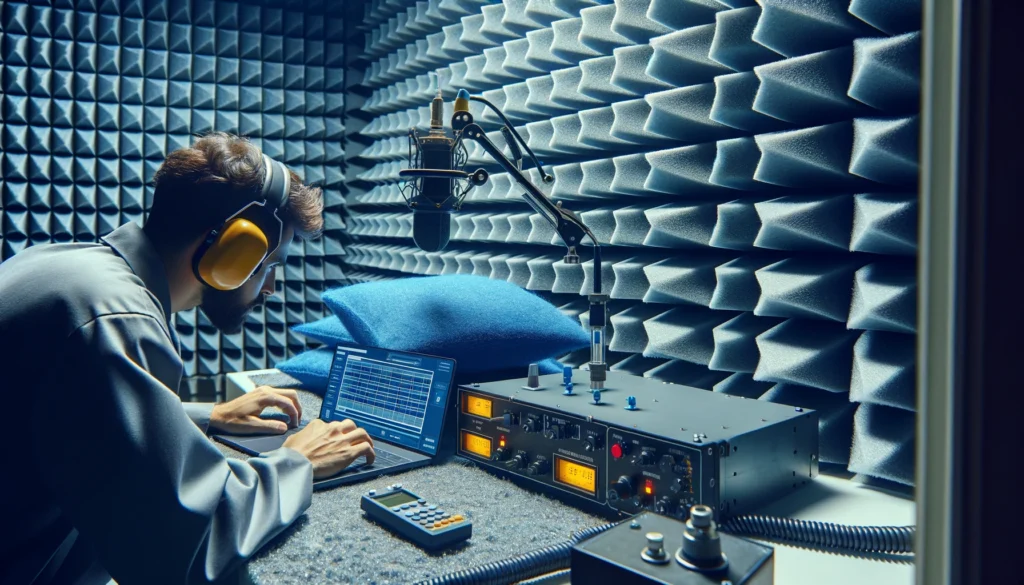
Extensive acoustic testing is performed on all foam products before distribution to customers.This verifies that the products meet strict noise reduction standards across desired frequency ranges.
The testing is conducted in specialized acoustic chambers using sound generators and measurement microphones.
Key aspects evaluated are sound absorption coefficients, noise reduction coefficient values, and mounting effectiveness.
Adjustments can be made to density, pore structure, flow resistivity, and thickness of the foam pieces to optimize acoustics.
Fire safety, emissions, and sustainability are also analyzed for certification compliance.
Cutting and Packaging
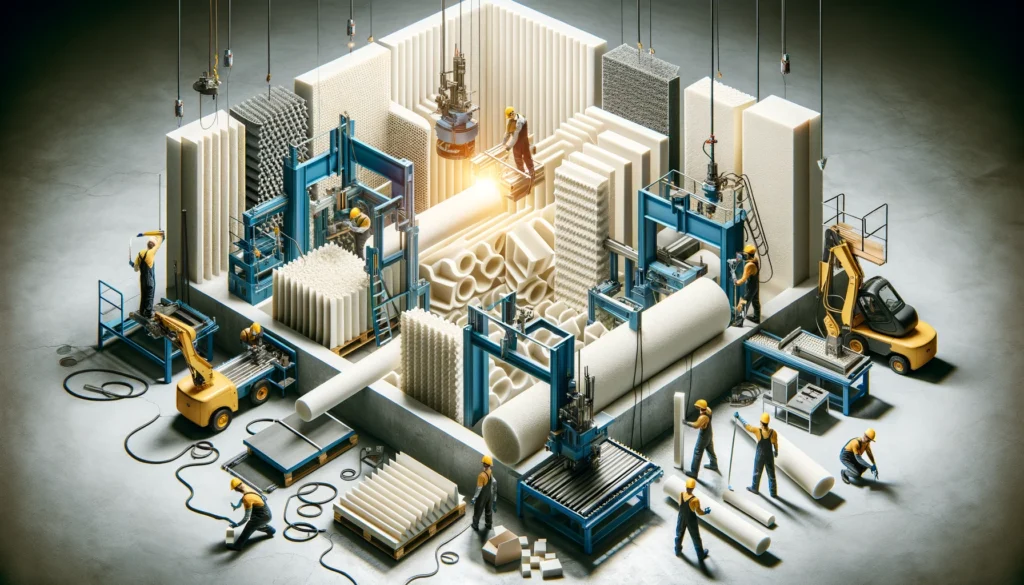
The very final steps in creating finished acoustic foam products are precision cutting and protective packaging.
Computer numerical control routers trim foam down to within a millimeter of specified dimensions for installation.
Precise sizing allows for tight seams and gapless mounting.
For shipping, acoustic foam must be carefully packed as it has flexible properties.
Packing methods include suspended bags, plastic sheeting wraps, foam edge guards, and placement inside rigid boxes.
If branding is desired, this is also when logos may be printed onto foam panels before packaging them up.
Conclusion
As we have seen, creating acoustic foam requires careful selection and processing of specialized materials using techniques like molding, curing, testing and cutting.
The versatility to craft forms with exact noise dampening properties gives acoustic foam the ability provide sound absorption in countless environments.
Understanding the manufacturing process allows designers to customize foam solutions to their unique needs.