Do you cringe when noisy upstairs neighbors wake you at night or traffic rumbles invade your home office? Finding the best insulation for soundproofing can transform noisy spaces into peaceful sanctuaries.
The optimal insulation for blocking sound includes fiberglass and mineral wool, when integrated properly to avoid flimsy installation issues undermining noise reduction.
Let’s explore the critical factors in selecting the right sound-blocking insulation and installation methods for your unique needs.
What Are The Types of Insulation Materials for Soundproofing?
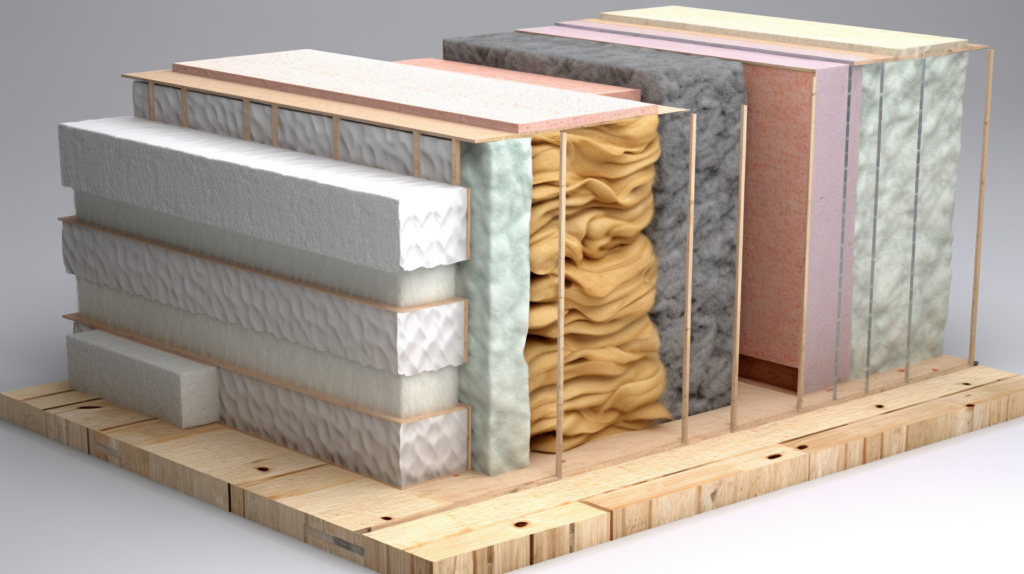
There are several types of insulation that can be used for soundproofing purposes. The most common options include fiberglass, mineral wool, cellulose, and spray foam insulation.
Each material has different properties that impact its effectiveness at blocking and absorbing sound.
Fiberglass insulation is an affordable and readily available option for soundproofing.
Fiberglass can be purchased in flexible batt insulation for walls and floors or as a loose fill insulation that can be blown into ceiling and wall cavities.
Fiberglass insulation works by absorbing mid-high frequency sounds and damping vibration that causes noise.
This helps reduce the transmission of airborne noise through walls, floors and ceilings.
The fibers in fiberglass insulation trap sound waves and vibrations, preventing them from passing through the walls and ceilings. This gives fiberglass insulation favorable sound dampening qualities.
Mineral wool insulation has similar sound absorbing properties compared to fiberglass insulation.
Mineral wool tends to be slightly more dense than traditional fiberglass insulation.
The higher density mineral wool bats and rigid boards fill framing cavities while leaving less excess space.
This density improves mineral wool’s ability to block structure borne vibration noise. Mineral wool insulation resists settling and compression over time very well.
So if properly installed, walls, ceilings or floors insulated with mineral wool retain consistent noise reduction ratings year after year.
Mineral wool is also praised for its beneficial fire resistance and water repellant traits. Making mineral wool a smart choice for exterior walls and basement soundproofing.
Cellulose insulation is a loose fill option made from recycled paper, cardboard and other fiber products.
While the recycled material composition is eco-friendly, cellulose requires very meticulous installation to avoid settling issues over time.
Settlement causes gaps in insulation which severely compromises noise blocking abilities. Even small gaps created by settlement can allow noise flanking around the insulation through the voids.
Cellulose also has a lower density and hardness rating compared to rock wool and rigid fiberglass. This means cellulose does not perform as effectively blocking the transmission of noise vibrations.
The loose fill method and tendency to compress down over time hinder cellulose as an ideal soundproofing solution.
Spray foam insulation starts out as quick-drying liquid. Installers spray the multi-component foam which then rapidly expands to fill any cracks, crevices and space in wall/ceiling cavities.
This helps eliminate small gaps that would otherwise form from cutting and placing traditional batt insulation.
However, spray foam insulation tends to be more expensive per square foot compared to other insulation types.
Certain formulations also use chemicals in installation that require personal protective equipment to apply safely.
Spray foam insulation is also unfortunately prone to cracking, shrinking and degrading over time.
This opens new air gaps as the foam ages, allowing increased noise to flank around the compromised insulation barrier.
What Are The Key Factors in Choosing Sound Insulation?
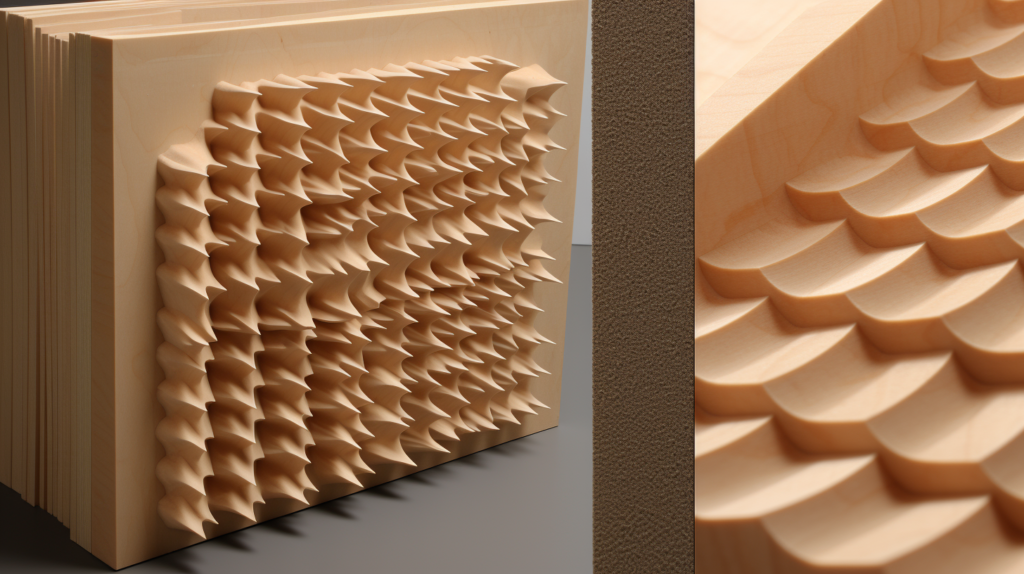
When selecting insulation materials for soundproofing projects, there are several key factors to consider besides just the type of insulation product alone.
The overall noise reduction performance depends greatly on the density rating, quality of installation, and strategic location/layering during application.
The density of an insulation product refers to how compact and tightly packed together the sound dampening materials are.
The higher the density rating of the insulation, the better able it is to effectively block sound waves. This is because dense substances make it difficult for noise vibrations to easily pass through.
So when choosing insulation, compare the product density specifications and opt for higher numbers. Those higher density ratings directly correlate with superior sound proofing capacity per inch.
Proper installation without gaps, spaces or compression is also imperative to achieve advertised noise reduction ratings from insulation.
Compressing insulation causes it to lose loft and density. Any gaps that form create a pathway for noise to flank around the insulation through the empty cavities.
Eliminating gaps during installation involves very precisely cutting insulation to fit exact measurements. Then tightly sealing edges with acoustical caulk prevents sound leakage.
Using appropriately sized insulation hangers also helps prevent compression over time. Taking these meticulous installation steps results in insulation that performs optimally blocking noise as intended.
Strategic location and layering of insulation also optimizes the noise dampening performance. Prioritizing adding insulation to exterior facing walls directly exposed to the outside dampens unwanted city noise like traffic.
Insulating ceilings below attics also greatly reduces rain and hail noise from overhead. Similarly, underfloor insulation placed under carpets and below sub-floors prevents noise transferring from foot traffic and furniture shuffling to rooms below.
Combining different insulation materials creates staggered stud or double wall assemblies that block considerable more noise than a single standard wall.
Putting layers like dense rigid insulation on exterior framing then adding fluffy fiberglass insulation inside doubles the soundproofing protection.
Best Insulation: Fiberglass Insulation Foam
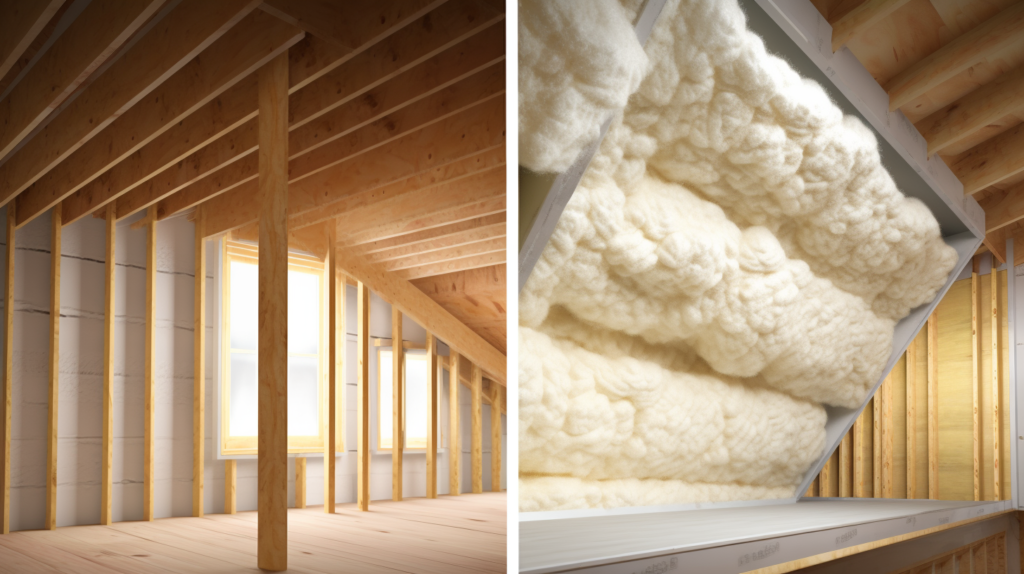
When weighing factors like availability, affordability and longevity of acoustic performance, fiberglass insulation emerges as a leading choice for do-it-yourself soundproofing projects.
Fiberglass insulation offers homeowners a cost-effective noise blocking improvement to apply on walls, ceilings and floor cavities throughout living spaces.
The widespread availability and competitive pricing of fiberglass insulation batts and loose fill make it a very approachable option for most sound dampening goals.
Big box hardware stores readily stock various sizes and types of fiberglass batting. Loose fiberglass also gets installed via blowing machine by many insulation contractors.
This easy accessibility allows homeowners to purchase materials conveniently and avoid special ordering.
In interior walls, dense fiberglass insulation effectively blocks noise transfer from room to room.
So bedroom walls insulated with fiberglass prevent sleep disruptions from home theater speaker sounds.
Fiberglass insulation placed underflooring beneath carpets also greatly reduces footfall noise and furniture shuffling sounds transferring to lower level rooms.
Proper fiberglass installation filling ceiling air cavities insulates from noisy rain, hail and roof vibrations. This helps maintain desirable indoor sound privacy in rooms overhead.
The actual composition of spun or woven glass fibers naturally absorbs and traps sound waves rather than transmitting acoustic energy.
This intrinsic physical property gives fiberglass insulation very favorable noise reduction ratings.
Additionally, proven long term stability means properly installed fiberglass insulation retains strong acoustic dampening performance year after year.
Avoiding shrinkage or breakdown makes fiberglass a sound investment lowering noise.
2. Mineral Wool Is Also Excellent
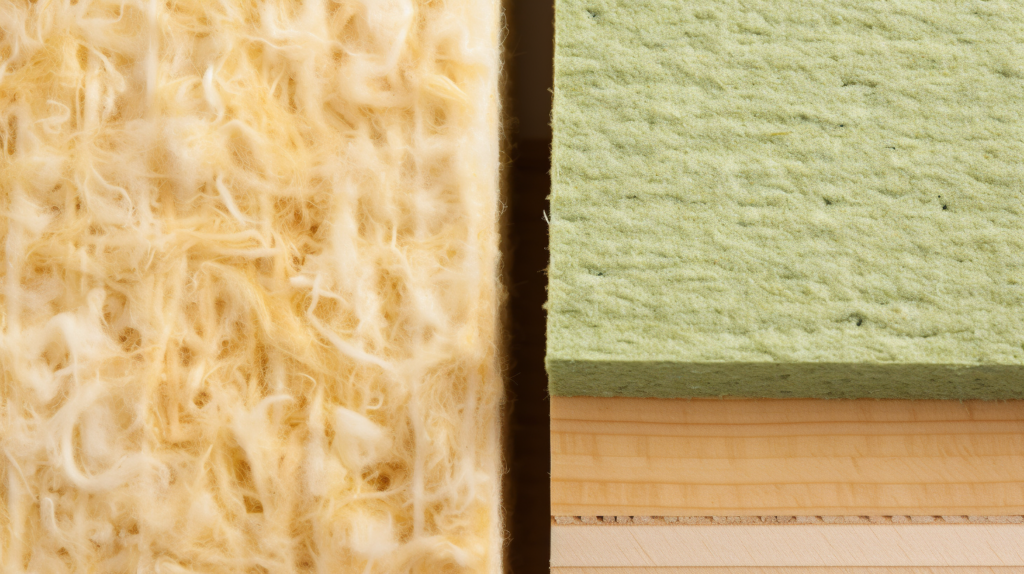
In many ways, mineral wool insulation offers comparable sound dampening abilities and installation methods to traditional fiberglass insulation.
Like fiberglass, mineral wool comes in familiar batts and boards suitable for retrofitting existing walls or placing during new construction. It shares excellent noise blocking capacities with fiberglass as well.
One area where mineral wool rates slightly better than its fiberglass counterpart is density per inch. Rock wool and slag wool compositions result in a naturally higher average density rating between R-3.0 to R-3.5 per inch.
This moderately higher mineral wool density measurably helps dampen noise vibrations better than less compact fiberglass.
So when space constraints dictate needing thinner insulation, mineral wool may provide a performance edge blocking noise.
Similar to fiberglass insulation, mineral wool insulation strongly resists settling, compression and maintains shape once installed correctly.
So over long periods, walls, ceilings or floors insulated properly with mineral wool retain consistent high noise reduction ratings.
Mineral wool insulation also shares the fire resistance and water repelling traits that make fiberglass suitable for exterior wall soundproofing projects.
Ultimately both traditional fiberglass and mineral wool serve as excellent insulation choices for noise blocking objectives.
For many applications the two materials have nearly identical acoustic dampening capacities. Mineral wool brings marginally better soundproofing only in particularly thin cavity scenarios.
While fiberglass maintains a slight value edge based on common availability and cost. But either one properly installed effectively reduces unwanted sound transmission.
Avoid These Sound Insulation Options
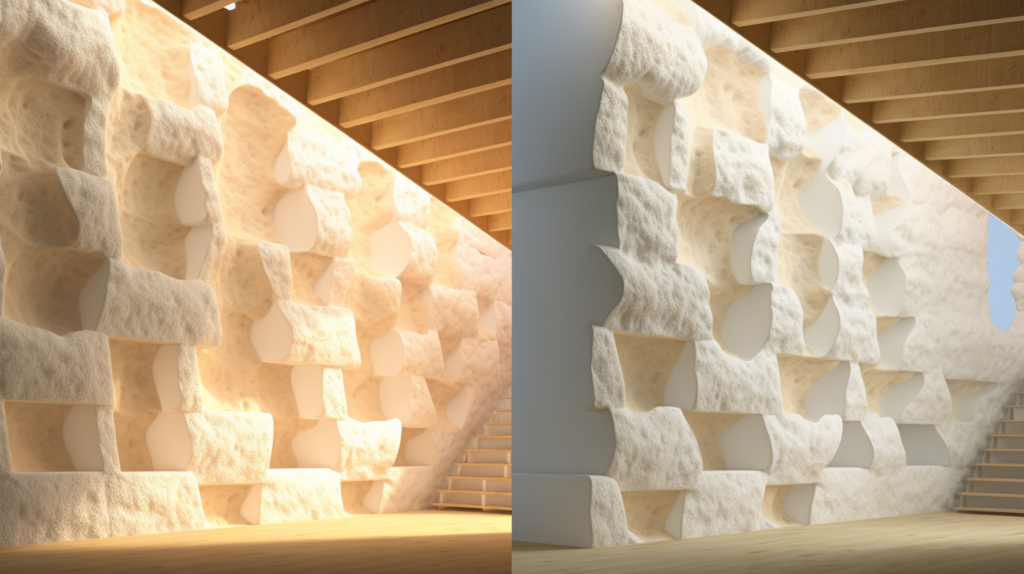
While fiberglass and mineral wool rate well as cost-effective sound blocking insulation choices, cellulose and spray foam come with more performance disadvantages.
Despite superficial appeal as affordable or gap-filling options, cellulose and spray foam lag behind mineral wool and fiberglass for noise reduction per inch.
One notable downside dampening enthusiasm for using loose fill cellulose insulation as a soundproofing solution is its tendency to settle unevenly over time.
The cellulose fibers, made from recycled paper and cardboard, compress down leaving noticeable air pockets and gaps towards the tops of wall cavities.
These new gaps allow considerably more noise flanking which compromises intended acoustic privacy. So while cellulose appears an affordable option meeting fire safety codes, the ongoing settlement and lower density are inferior for stopping noise.
Spray foam insulation also carries some insulation credentials that seem attractive upfront. It can fill the smallest gaps and crevices which helps eliminate noise leakage points.
However spray foam carries significantly higher material costs per square foot compared to traditional insulations.
Certain less eco-friendly formulations also use hazardous chemicals requiring protective gear during application.
And once installed, foam insulation shrinkage can introduce new air gaps in the coverage that let sound transmission return.
Early cracking or breakdown starts to diminish noise reduction not long after installation.
Factoring in higher price, chemical off-gassing and gradual performance decline – cellulose and spray foam lag as top soundproofing recommendations.
Ultimately denser, more stable traditional insulation materials bring better long term acoustic insulation pound for pound.
So skipping these alternatives in favor of time-tested fiberglass or mineral wool makes more sense for permanent noise relief.
Proper Installation Matters Most
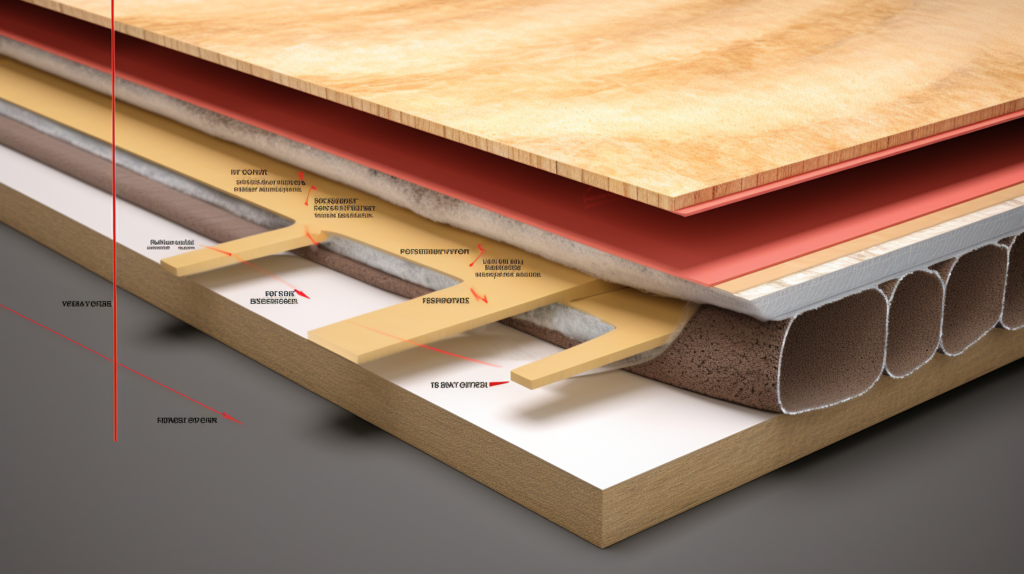
Despite the clear advantages of fiberglass and mineral wool insulation stopping noise, installation missteps can still hinder results.
If gaps, spaces or compression issues arise with either material, excess noise inevitably intrudes.
So accurate cutting, secure backing and seam sealing all make big impacts achieving real-world soundproofing for homeowners.
Being mindful to avoid gaps when installing insulation improves noise blocking performance. Taking careful measurements then precisely cutting insulation to fit tightly is crucial.
Gaps as small as a 1/4 inch allow noticeable noise flanking around the insulation.
Compressing thick insulation like batts above 20% also causes worsened density and acoustic dampening capacity over time.
Using correctly sized insulation hangers adds important backing support minimizing compression risks.
Sealing all seams and edges thoroughly with acoustical caulk also prevents sound leakage. The specialized caulk fills even microscopic junctions completely rather than leaving voids.
Carefully caulking the linear gaps between walls, ornamental corners, electrical fixtures and more ensures air tight insulation installation.
Without comprehensive caulking, noise inevitably finds pathways bypassing insulation traveling through overlooked cracks.
Adding mass in the form of extra layers of drywall can make substantial impact damping noise too.
Using specialized resilient channels to detach drywall sheets from wall studs improves damping. The channels create a tiny decoupled air gap which improves noise blocking.
Applying two or even three layers of drywall screwed securely to these channels noticeably reduces unwanted sound transmission.
So truly optimizing insulation’s noise reduction capacity relies on competent installation practices.
Careful attention to detail eliminates gaps while caulking and drywall application enhances soundproofing performance.
This allows fiberglass or mineral wool insulation to achieve maximum acoustic benefit blocking annoying noise.
Conclusion
Properly installed fiberglass or mineral wool insulation provides the most cost-effective and long-lasting noise reduction for homeowners.
Strategic application combined with meticulous air sealing allows these materials to effectively block unwanted sound transmission.
Avoid settling for less effective insulation options or letting poor installation undermine acoustic performance.
Follow these best practices outlined to choose the ideal soundproofing insulation for your needs.