Is felt really the miracle material for soundproofing your noisy spaces as some claim?
The short answer is no – felt actually fails as an effective sound barrier despite its popularity.
Let’s dive in to understand exactly why felt doesn’t work for soundproofing and explore better alternatives.
Why Felt Is Not An Ideal Material For Soundproofing

No felt is not good for soundproofing.
Felt lacks the mass and density needed to effectively block sound transmission.
On its own, felt is too thin to prevent noise from passing through. The porous, fibrous structure of felt makes the material ineffective at impeding vibrations.
Felt has gaps and pores that allow sound waves to easily pass through. For these reasons, felt should be avoided as a primary soundproofing material.
Ideal soundproofing materials share attributes like density, mass, rigidity, and thickness that are lacking in porous felt.
Density describes the compactness of a material’s molecules. Denser substances have tighter molecular structures that do not compress as easily. This makes them more effective at blocking noise vibrations.
Mass correlates strongly with noise reduction because heavier materials literally weigh down on sound waves. Mass measurably impedes vibration transfer.
Greater mass also reflects more of the noise energy back rather than letting it pass through. This is why heavyweight concrete can achieve an STC rating over 50, while felt scores nearly 0.
Rigid materials with little flexibility also outperform felt for soundproofing. If a substance can vibrate freely and bend, it will inevitably allow some noise energy to transmit.
Walls sheathed in multiple layers of drywall resist vibration far better than thin felt. The stiffness reflects sound rather than absorbing any vibrations from noise.
Thickness plays an important role too, as thicker materials provide more opportunity to impede sound waves passing through.
But density and mass have a far greater impact, as even a thick layer of felt cannot match a thin sheet of MLV for blocking noise.
Prioritizing density and mass over raw thickness will lead to better noise reduction.
Understanding these physical properties provides guidance for selecting ideal soundproofing materials. Felt lacks the density, mass, rigidity, and thickness required to isolate noise.
That is why acoustic engineers never rely on felt alone for proper sound isolation.
Advanced soundproofing calls for materials engineered like MLV to achieve lab-tested noise reduction that porous felt simply cannot deliver.
Why Felt Fails For Soundproofing

When used alone, felt does not have the physical attributes needed to achieve proper sound isolation.
Felt on walls or ceilings will not prevent noise flanking, which is when sound travels around containment through paths of least resistance.
Flanking is a major issue that renders attempted soundproofing ineffective. Felt allows flanking by leaving gaps wherever it does not fully cover a surface.
The thin and light nature of felt also means it is unable to achieve meaningful STC (Sound Transmission Class) or NRC (Noise Reduction Coefficient) ratings.
These scientific ratings measure a material’s effectiveness at blocking airborne sound and absorbing noise, respectively.
Quality soundproofing materials can reach STC ratings in the 50s or 60s, while felt would achieve an extremely low STC rating indicating poor sound blocking.
Whether the noise source is footsteps above, voices next door, or loud appliances, felt does nothing to provide a true barrier.
The sound waves easily pass through the thin fibers, vibrating the material with little impedance. Felt lacks the mass and rigidity required to reflect noise.
Only denser materials can effectively stop impact and airborne noise transmission.
While felt may absorb some high frequency sounds to a minor degree, its porous structure prevents it from sound isolation.
The many pores and gaps allow noises to flank around the material. If the goal is blocking sound rather than muffling echo, felt will utterly fail to achieve adequate soundproofing.
1. Felt Fibers Are Too Thin And Porous To Block Sound
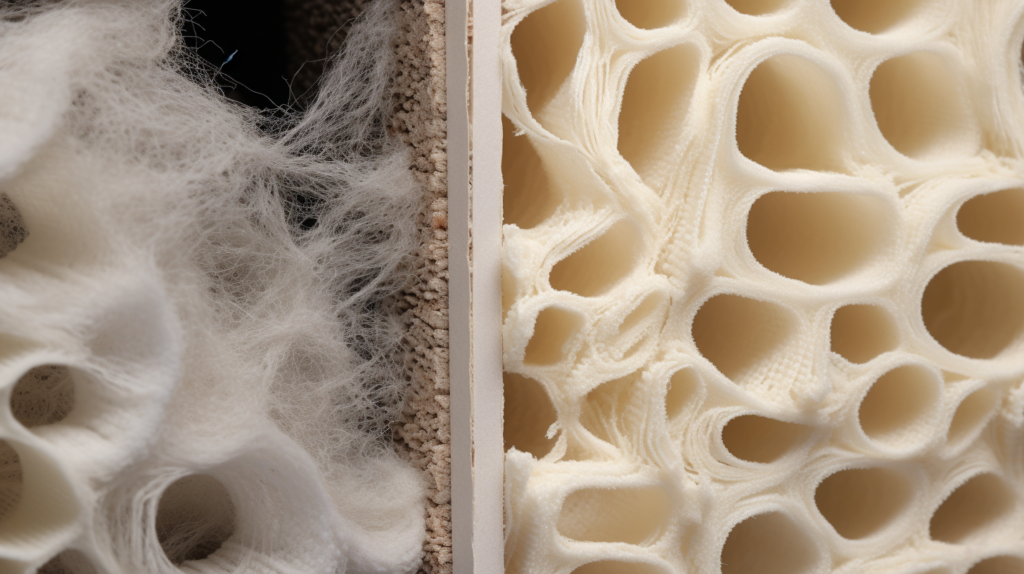
The naturally porous structure of felt makes it unsuitable for preventing noise transfer. The individual fibers that comprise felt are thin and feature many tiny gaps between them.
This gives felt an airy, flexible texture that lends itself well to crafts and insulation. However, those same traits mean felt cannot impede sound waves.
Felt’s porousness lets noise easily penetrate the material rather than reflecting off its surface. Testing has shown that felt offers almost no resistance to the transmission of sound energy.
Without sufficient mass or density, the fibers and gaps simply vibrate and allow noise to pass unimpeded regardless of felt’s thickness.
Whether made from wool, synthetic blends, or recycled materials, all felt shares this porous quality that renders it ineffective at blocking sound.
Noise caused by voices, footsteps, mechanical equipment, and more can penetrate felt as if it were barely there.
Even just a single layer of drywall outperforms felt for soundproofing thanks to greater density.
At best, standard felt may absorb small amounts of high frequency noise like echo and reverberation. But any meaningful soundproofing requires blocking lower frequencies too.
Heavier footsteps and raised voices generate low-end noise that bypasses thin felt completely.
Only materials formulated specifically for noise control, like MLV, have a chance at absorbing low-frequency sounds.
For these reasons, contractors and acoustical engineers never rely on felt as a component in soundproofed assemblies.
The fundamental weakness of felt for impedance and noise blocking means it plays no beneficial role in proper sound isolation.
The fibers and porous nature enable flanking while failing to achieve meaningful sound transmission reduction.
2. Felt Does Not Prevent Flanking Noise Like Real Soundproofing
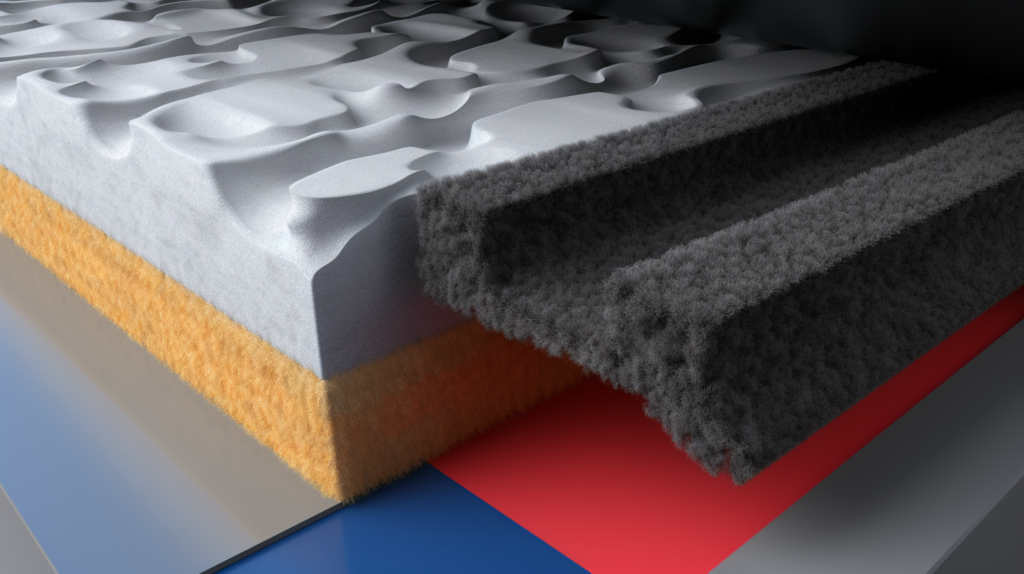
One notorious weakness of felt as a soundproofing material is its inability to prevent flanking noise transmission.
Flanking occurs when noise travels around a blockade through gaps and weak points in the structure. Even if felt covers a ceiling or wall, it does nothing to stop flanking through adjoining areas.
Highly porous materials like felt enable flanking because they are so easily penetrated. Unblocked flanking paths provide an easy route for sound waves to circumvent an attempted sound barrier.
Noise will naturally take any open side passages around an obstacle. So if felt leaves structural gaps unfilled, it fails to achieve isolation.
Effective flanking prevention relies on comprehensive coverage and sealing of potential sound leakage points.
Acoustical caulk, sealants, and gaskets must be applied around outlets, windows, vents and any gaps. Felt lacks the density and rigidity to thoroughly plug these flanking opportunities.
Stopping flanking necessitates blocking all vibrations through the surrounding structure.
Only lab certified assemblies of multiple blocking, sealing, and absorbing layers can achieve meaningful flanking noise reduction.
No single material alone, especially light fibrous felt, stands a chance at preventing flanking.
Proven techniques like staggered studs, double drywall, insulation, MLV, and isolation clips work unison to seal flanking paths. Felt in isolation is no match for persistent sound waves.
In summary, porous materials like felt enable continued noise disruption through inevitable flanking pathways in a building.
True acoustical isolation requires the combination of blocking, absorbing, and sealing materials to cut off all sound leakage.
As an airy, porous substance, felt fails to meet these stringent requirements for flanking prevention that proper soundproofing demands.
3. Voices And Footsteps Easily Penetrate Thin Felt
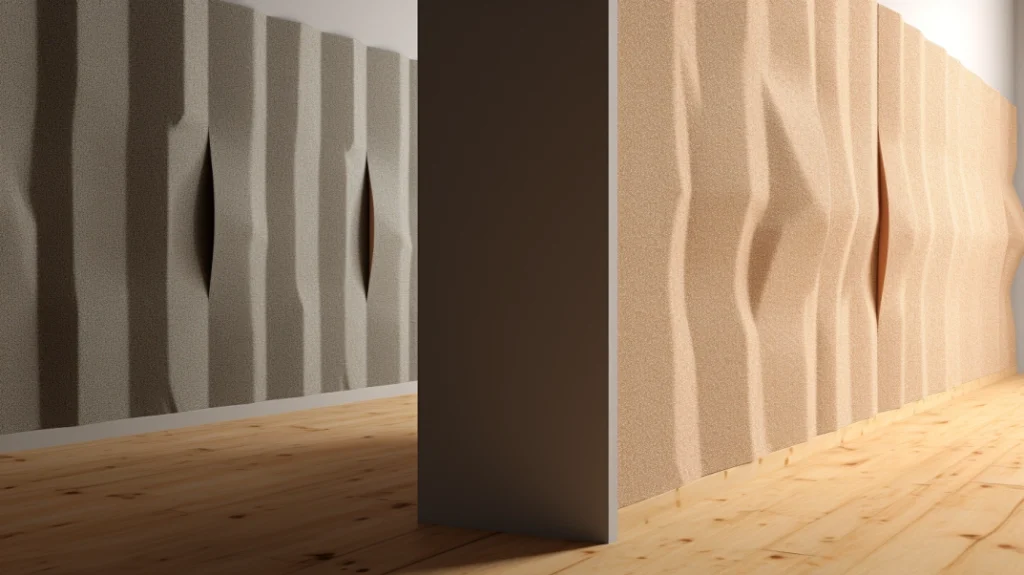
Two common sources of disruptive noise in homes and offices are voices and footsteps. Unfortunately, the thin and porous nature of felt renders it useless for blocking noise from voices or foot traffic.
Human speech and walking impact noises easily bypass thin felt with no appreciable reduction in volume.
The wide range of audible frequencies in human speech can penetrate felt as if it were not even present. Even loud voices coming through walls can overwhelm flimsy felt insulation.
Without sufficient density to dampen and isolate vibrations, felt allows spoken words to transmit with clarity.
Footstep impact noise is also barely impeded by thin felt coverings. The felt fibers and gaps flex with each stomp or heel strike, allowing the energy to freely pass through.
Hard surfaces coupled with felt will do little to muffle noise from kids running overhead or the stomping of hard-heeled shoes.
Advanced soundproofing materials like MLV are specially engineered to dampen a wide range of noise frequencies.
Membranes containing dense minerals and polymers can significantly reduce the transmission of voices, footsteps, and other common annoyances.
Multiple noise blocking and absorbing layers work in combination to cut ambient noise passing through.
But as a single thin layer, options like basic felt provide no meaningful resistance against the vibrations and frequencies within human voices or footsteps.
Heavy walking and loud talking can easily overpower the limited noise absorption capabilities of porous, flexible felt. Proven sound isolation requires durable materials with density, not flimsy fibers alone.
4. HVAC Systems And Appliances Require Dense Materials, Not Porous Felt
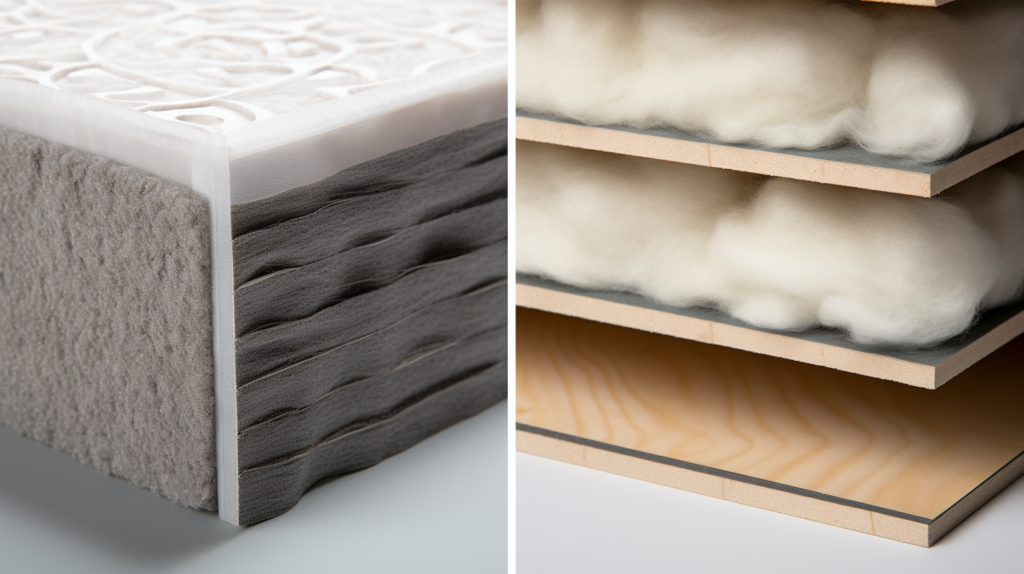
Another use case where felt fails for soundproofing is around noisy appliances, HVAC systems, and mechanical equipment.
Whether it’s a rattling furnace, loud fan, or vibrating washer, felt will not adequately dampen and isolate this equipment noise. Materials with proven density are required for a noticeable difference.
HVAC systems and ducts transmit noise throughout a structure, especially when the vibration of airflow causes sheet metal to rattle.
Lining ducts with felt may muffle some high pitches, but deeper fan and airflow rumbling easily penetrate the thin insulation. MLV or dense rubber lining works better for blocking duct noise.
Home appliances also generate problematic vibration and noise spanning a wide frequency range. Felt wrapped around a washer, dryer, or refrigerator will hardly muffle the sounds enough for comfort.
The appliance’s vibrations will flex and pass through the felt, especially lower frequencies. Layered MLV, plywood, and insulation make a superior noise barrier.
For any mechanical room, equipment coverings require substance to prevent noise flanking. Felt loosely draped over a motor or generator provides no isolation against structure-borne vibration and flanking noise.
Effective circulation fans, turbines, and compressors benefit from rigid acoustic covers, not flimsy porous felt alone.
What Are The Alternatives To Felt For Soundproofing?
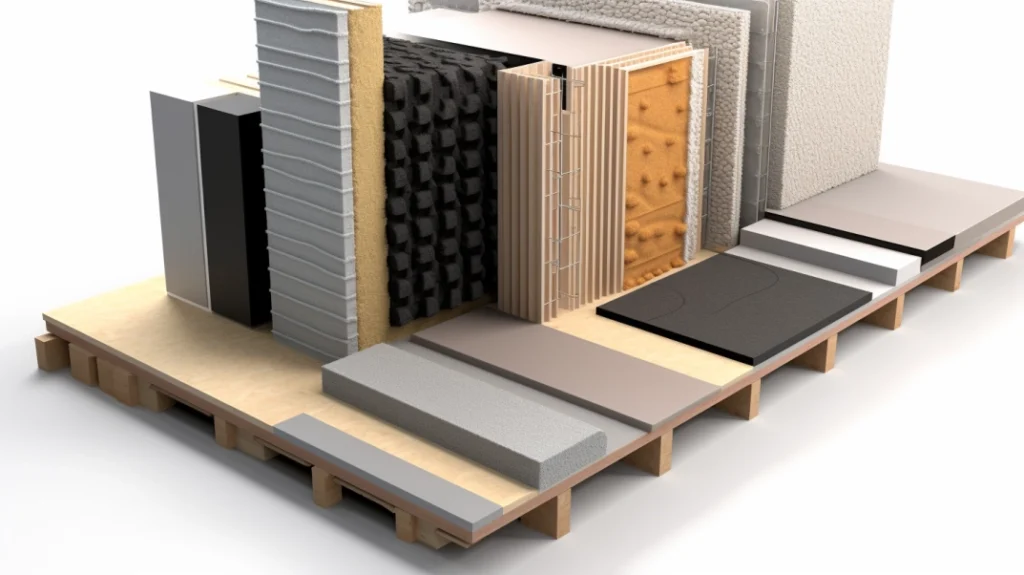
An option for adding mass to walls and ceilings is using flexible soundproofing foam or batt insulation made from mineral wool or fiberglass.
These are thicker and denser than felt, thus much more effective at impeding noise. The material can be cut to fit inside wall cavities, attics, and floor joists.
Combining insulation with MLV creates an effective noise barrier.
Resilient channels are metal runners that can be installed perpendicular across studs or joists before drywall. This decouples the drywall from the framing, allowing it to vibrate independently.
Sound transmission is reduced as the channels dampen vibrations in the wall assembly. Multiple layers of drywall screwed into the channels adds even more mass.
For maximum noise control, a staggered stud partition system can be constructed. This involves double rows of staggered wall studs with insulation between them.
By separating the studs and eliminating any direct contact between interior and exterior wall surfaces, noise transfer is drastically minimized.
Staggered stud walls represent the gold standard in soundproofing assemblies.
Whether applied to existing construction or new builds, these soundproofing techniques all come down to establishing barriers with the density and mass that felt lacks.
Any gaps or joints must be thoroughly sealed with acoustical caulk and foam to prevent flanking.
Combined, these materials create lab-tested, proven noise control far beyond the capabilities of felt alone.
Conclusion
In conclusion, felt is simply not an effective material for proper soundproofing.
Its porous structure allows noise to easily penetrate, flank around, and transmit through the thin fibers. Solid sound isolation requires density, mass, rigidity, and thickness that felt lacks.
While felt can muffle echo, true acoustic separation depends on purpose-engineered materials like MLV, staggered stud walls, double drywall, and sealed insulation.
For guaranteed noise reduction, rely on lab tested assemblies, not flimsy DIY felt alone.