Do your studio’s foam acoustic panels seem less effective at absorbing sound after a few years? Many studio owners underestimate the typical lifespan of these sound dampening panels.
So how long does a foam acoustic panel actually last before needing replacement? Let’s dive in to find out…
A foam acoustic panel’s lifespan depends on density, material composition, and environmental factors – with higher quality panels in climate controlled spaces lasting 2-5+ years.
In this comprehensive guide we’ll outline foam panel durability considerations, lifespan maximization tips, signs of deterioration, and typical replacement costs studio owners face over time.
How Long Does a Foam Acoustic Panel Typically Last?
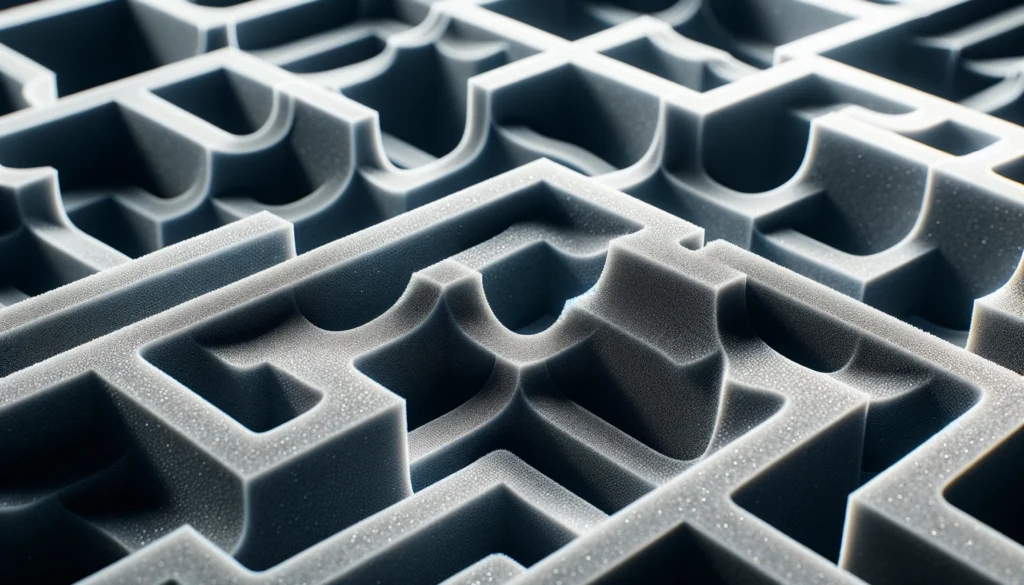
A quality foam acoustic panel with proper care typically lasts between 2-5 years before needing replacement.
Lightweight, low-density panels deterorate faster while durable melamine and polyethylene foam lasts longer.
We’ll explore the key factors influencing lifespan in more detail below.
What Are Foam Acoustic Panels?
Foam acoustic panels are panels made out of open cell foam that are used to help absorb sound in a room in order to improve the overall acoustics.
Acoustic foam panels are typically made out of soft materials like polyurethane foam or melamine foam and work by absorbing sound energy rather than reflecting it, helping to reduce echoes and reverberation.
The open cell structure inside acoustic foam panels helps to trap sound waves and convert the audio energy into heat rather than reflecting it back into the room.
This allows the foam to ‘dampen’ the acoustics and diminish excess reverberation.
Acoustic foam panels achieve sound absorption through their porous surface and flexible cellular inner foam structure.
As sound waves strike the yielding surface of the acoustic foam panel, the vibrations get dispersed into the panel rather than bouncing back into the room.
By installing foam acoustic panels on key surfaces like walls and ceilings, the reflective quality gets minimized, resulting in far less echoes and ambient reverberation in the space.
This leads to much clearer and concentrated audio clarity within the room, especially helpful for recording studios and listening spaces where quality sound reproduction is essential.
Typical Lifespan Of Acoustic Foam Panels
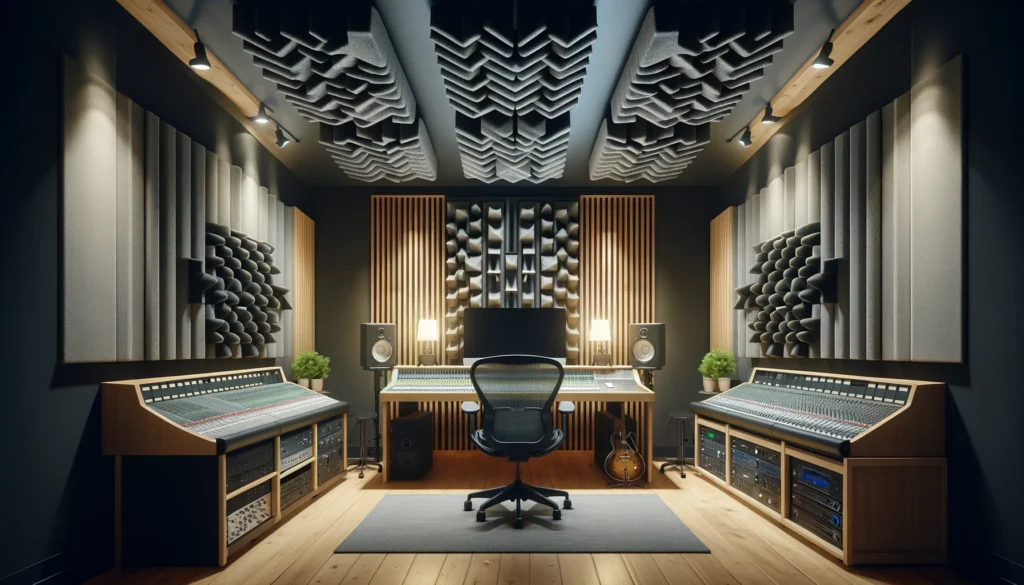
The typical lifespan of acoustic foam panels under normal use tends to fall somewhere between two to five years.
However, the actual lifespan can vary rather significantly depending on several important factors influencing the usable durability of the foam over time.
One of the most important durability factors is the density rating of the acoustic foam itself.
Higher density acoustic foam, usually with a density around 1-2 pounds per cubic foot, will last considerably longer than low grade, light density foam which may deteriorate after only 1-2 years.
Higher density foam is inherently more rigid and structurally durable.
It withstands the constant impact from sound vibrations much more readily and resists breakdown over repeated sound absorption use cycles.
Lower density acoustic foam is more malleable and flexible by design, yet lacks the long term resilience needed for lasting performance over years of exposure.
Low grade polyurethane foam in particular compresses easily under sound loads, leading to permanent deformation and cellular breakdown internally within the foam that causes tearing, cracking and crumbling precipitously faster than denser alternatives.
Environmental factors also play a pivotal role in longevity equation for foam panels.
Excess humidity, temperature fluctuations, sunlight exposure, and dust build up can markedly accelerate the decay and breakdown of acoustic foam materials, severely shortening usable life span compared to panels used in optimized studio environments.
Foam panels used in climate controlled studios with regulated humidity and temperatures will enjoy a much lengthier usable lifespan compared to panels placed in unconditioned basement studios prone to moisture accumulation and mildew growth.
Maximizing The Lifespan Of Your Panels
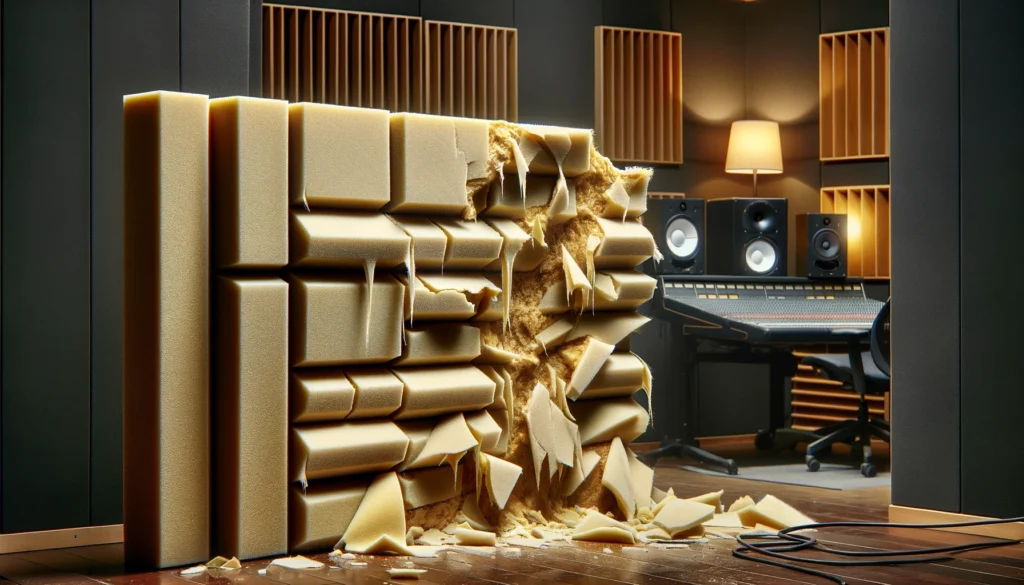
To maximize the functional lifespan of your acoustic foam panels, starting with quality foam is imperative.
Seeking out higher density polyethylene or melamine foam panels rated at 2 pounds per cubic foot density or greater will best withstand continuous sound dampening duty without premature failure compared lower grade polyurethane and composite foam options more vulnerable to breaking down.
In addition to foam density and type, selecting acoustic panels with properly engineered outer coatings extends durability against environmental threats.
Makers offering foam panels with protective sealed outer layer barrier skins that shield the inner foam from dust and humidity penetration meaningfully protects internal foam cell matrix from degrading.
These enhanced surface layers prevent dirty build up inside the foam which can undermine acoustic performance over shorter time frames.
Proper placement decisions when installing foam panels also prevents avoidable environmental damage shortening panel life expectancy.
Be sure to affix panels in optimal room locations away from direct sunlight exposure wherever possible.
Direct UV rays oxidize foam cellular structures faster than indirect light.
Temperature and humidity controlled spaces are additionally ideal for maximized longevity as fluctuations introduce expansion and contraction cycles that progressively weaken foam composite cohesion over recurring exposures.
Regular maintenance helps uphold integrity longer as well.
Periodically running a soft brush nozzle vacuum attachment over panels clears away accumulated particulate debris from settling into surface pores or gaps in the foam where they undermine framework stability.
For deeper cleaning needs, a gentle wipe down with soft damp microfiber cloth removes stubborn surface dust buildup without over-saturating panels.
Let panels completely dry prior to remounting using adhesive strips or clips to avoid any moisture related issues.practices coupled with infrequent handling prevents causing unnecessary compression, tears, punctures or bent panels which adversely impact acoustic performance.
Panels secured properly to walls and ceilings will maintain useful integrity considerably longer than loose panels which risk over-shifting.
Signs Your Panels Need Replacing
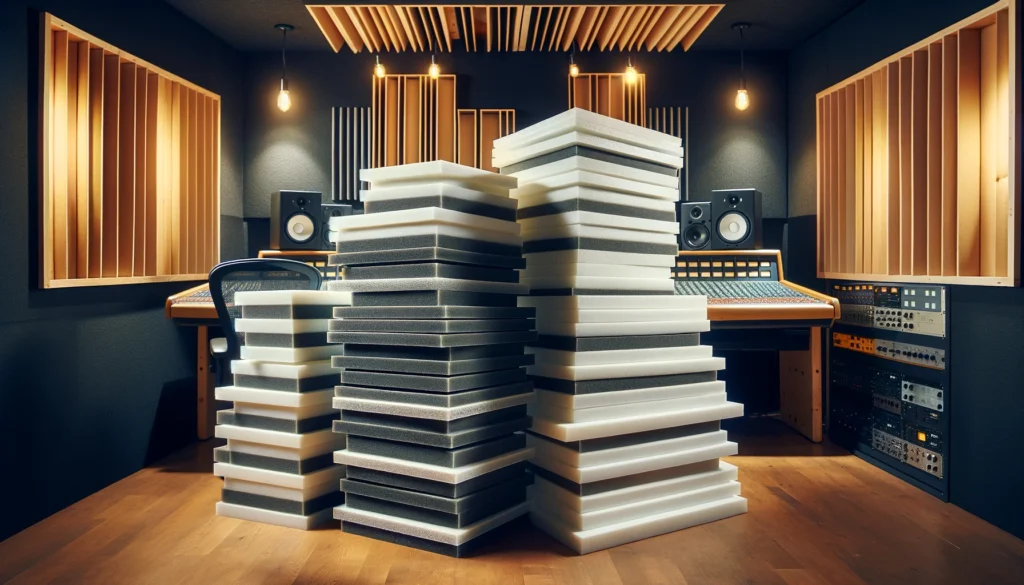
There are several clear cut warning signs to routinely evaluate when assessing whether your specific acoustic foam panels require replacement.
Visually inspect panels for peeling or cracked outer barrier coatings which expose vulnerable inner foam layers to infiltrating elements that then accelerate sound deadening deterioration.
Additionally, visible tears, perforations, holes or severely bent areas undesirably allow sound waves to pass straight through panels rather than getting absorbed efficiency within the foam matrix as intended.
Touch test acoustic panels periodically feeling for softened segments or permanently limp, misshaped spots that no longer rebound back after compressing.
These deformed areas indicate overloaded foam capacity losing resiliency from overloaded use or environmental moisture damage.
Lack of spring back confirms capacity limits reached necessitating substitution to restore acoustics.
Likewise, pay close attention to any noticeable decline in perceptible sound dampening quality within the room, particularly increased echo problems returning.
This points to panels no longer effectively absorbing and dissipating sound waves as designed.
If foam crumbles or falls apart easily by hand, immediate replacement is required before additional sound wave amplified damage spreads across adjoining foam segments.
Finally, when panels accumulate heavy, visible layers of opaque dust and dirt or debris unable to be properly vacuumed and cleaned off despite multiple attempts, replacement becomes necessary at that stage.
Soiled particle build up fouls porous foam surface areas keeping them from correctly attenuating sound waves.
So restoring full acoustic performance quality in the space requires installing fresh new foam panels.
Typical Costs For Replacement
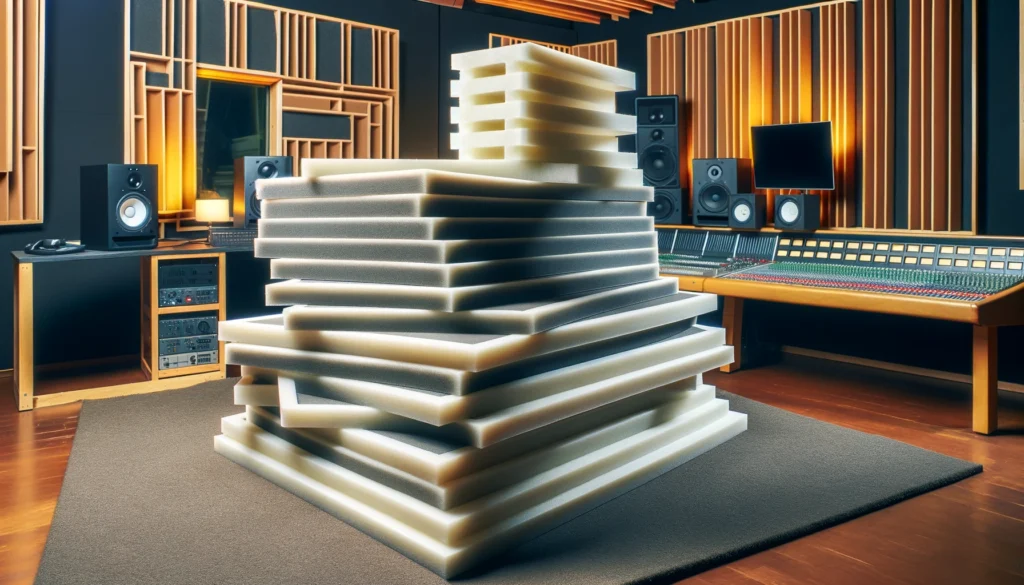
Actual replacement costs for new acoustic foam panels varies substantially depending on type, size, density rating differences, and overall quality disparities between foam products on market.
Cost factors also change based on total number of panels required for a given room space application.
However, some general cost guidelines help set reasonable expectations when budgeting for periodic foam panel replacements.
Basic acoustic foam tiles sized around 12” x 12” retail on average between $10-$30 per tile panel depending on thickness, foam grade, and competitive pricing specials across suppliers.
These economy tiles normally offer limited acoustic effectiveness for a year or two before requiring substitution.
Mid-grade polyurethane foam tiles sized similarly might run $20-$50 for improved performance properties.
For professional studio level projects, upgraded melamine or polyethylene replacement panels sized 2’ x 4’ with Class A flame retardant ratings routinely retail between $50-$100 per high quality piece.
These investable panels last considerably longer thanks to durable composition and density ratings meeting or exceeding 2 pounds per cubic foot.
In addition, full room acoustic sound treatment endeavors ranging from professional recording studios to home based setups must factor the final accumulated budget over multiple generations of foam panels.
Given average foam lifespan realities, studios undergo at least one to two rounds of foam replacements over a typical 5-10 year operating history.
Even personal home studios on limited budgets spend several hundred dollars over time when totaling up costs for continually upgrading foam acoustic solutions.
So prepare sufficient replacement budget for preserving your studio sound integrity.
Conclusion
In summary, studio-grade acoustic foam panels generally last between 2-5 years or more with proper care and optimized conditions.
Key factors of density, outer coatings, controlled climate, and gentle handling all extend usable lifespans closer to the 5 year range before performance declines necessitate new panel investments.
Stay alert for signs of deterioration and budget sufficient replacement funds to preserve your studio sound integrity over the long run.