Does stuffing sponge into cracks and crevices actually manage to soundproof your surroundings?
The porous structure of sponge can absorb small amounts of noise but lacks the density and durability to broadly prevent sound transmission.
Let’s dive into why sponges come up short on the rigorous demands of quality acoustic insulation and the better alternative options available.
Is Sponge Good For Soundproofing?
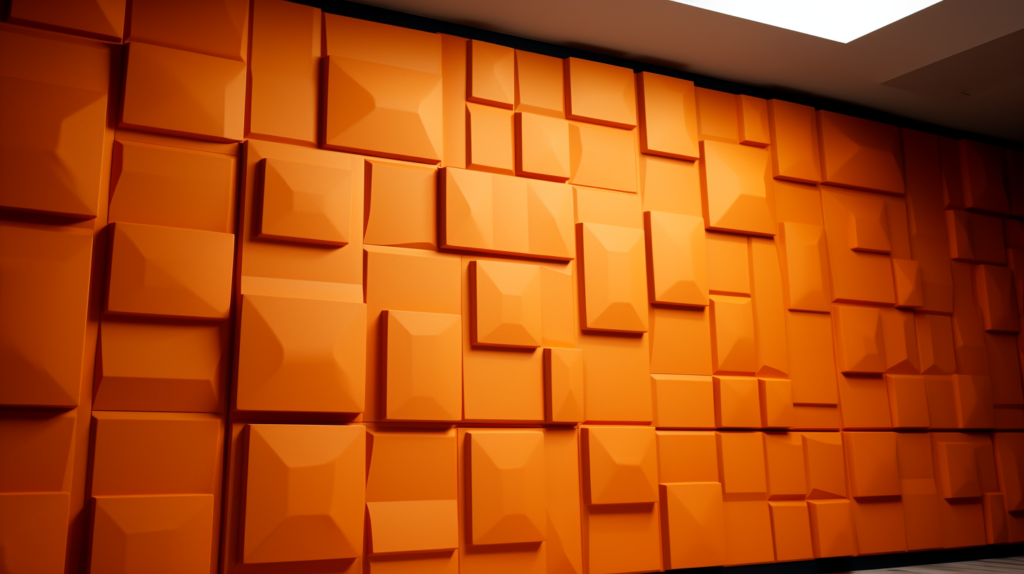
No, sponge is not good for soundproofing. The porous nature of sponge is better at absorbing small amounts of ambient noise rather than blocking meaningful noise sources.
Sponge lacks the density required to effectively prevent the transmission of sound waves through wall cavities and around door joints.
Using sponge alone to soundproof a room would provide little noticeable reduction in noise levels.
While sponge does dampen some high frequency sounds through absorption, it does not address lower frequencies that transmit easily through structures.
Sponge can compress over time and allow sound to pass through gaps that develop. Exposed sponge also runs the risk of harboring mold and mildew with excess moisture.
For proper sound blocking, purpose-built materials like mass loaded vinyl and insulation are far superior options.
Why Sponge Does Not Work For Soundproofing Purposes
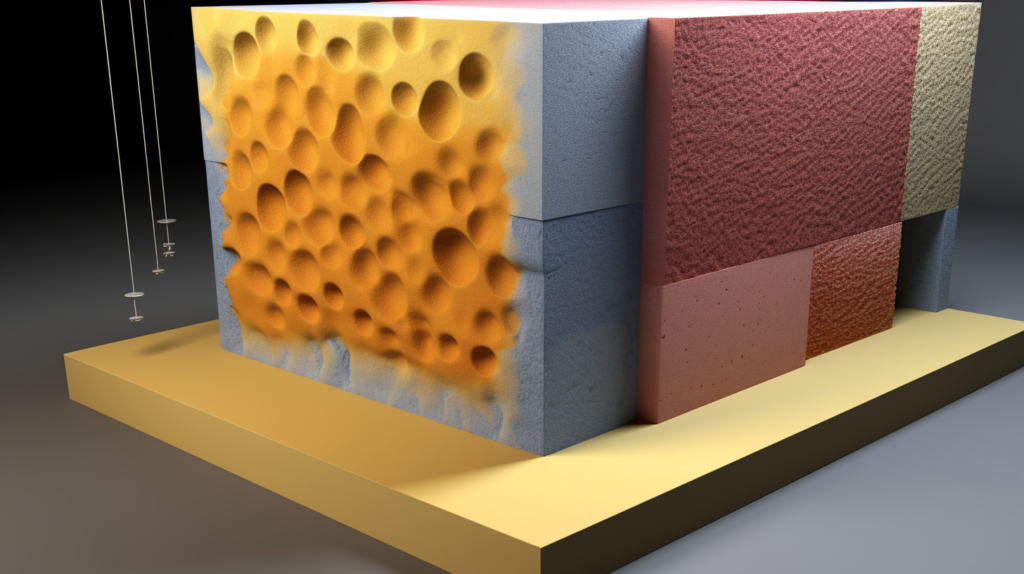
Sponge lacks the fundamental qualities needed for blocking audible sound transmission. The open and porous nature of sponge enables absorption of sound waves through slight dampening.
However, the soft spongy texture readily compresses, which limits meaningful noise reduction between adjoining rooms or outside noise permeating into interior spaces.
Insufficient Density Of Sponge
Sponge has an open and porous cell structure which gives it the squishy texture. But this porous texture prevents sponge from having enough density and rigidity to obstruct impactful sound waves.
High frequency noises may get slightly muffled, but louder low frequency noises have enough energy to induce vibrations that easily transmit through sponge.
This makes sponge ineffective for noticeably reducing noise levels.
Compromised Performance Over Time
While sponge can seem snugly fit into cracks and gaps initially, the soft texture compresses readily. Over days and weeks, compression and natural drying of the sponge material degrades the tight seal.
Gaps form allowing easy passage of noise negating any sound dampening gains that sponge may have briefly provided.
The diminished blocking performance means sponge is only useful as temporary soundproofing at best.
Susceptibility To Moisture Damage
Sponge placed in enclosure areas means exposure to natural humidity and also higher chances of water contact from leaks.
The porous foam structure absorbs ambient moisture readily leading to faster deterioration and compression set.
Prolonged moisture also encourages mold growth within sponge that is unhealthy.
This moisture vulnerability limits sponge’s appeal for permanent indoor soundproofing needs compared to water-resistant alternatives.
What Are The Alternatives To Sponge For Soundproofing
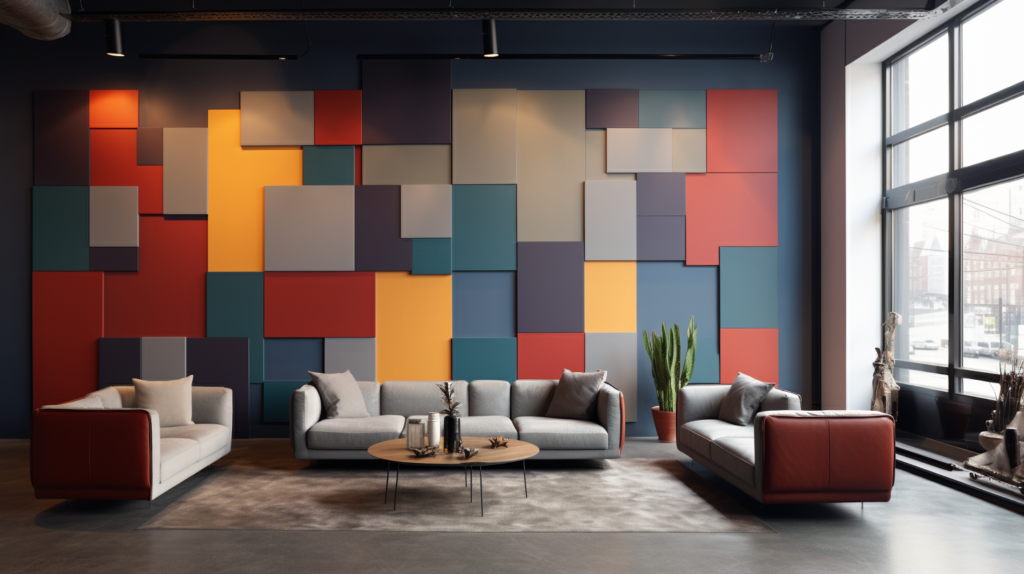
Purpose-built soundproofing materials provide vastly superior noise blocking capabilities compared to sponge.
Options like mass loaded vinyl sheets, insulation, and sealants withstand compression, resist moisture, and obstruct impactful noises across a broader frequency range.
Acoustic Insulation
Materials like fiberglass and mineral wool efficiently absorb noise while also impeding sound transmission.
The fine fibrous structure traps sound waves while the packed density resists vibration transmission.
Insulation combines noise absorption with significant decibel level reductions and maintains performance reliably long-term when professionally installed.
Mass Loaded Vinyl
Mass loaded vinyl (MLV) leverages density to block noises effectively.
The heavy flexible vinyl sheeting contains barium salts or other mineral fillers to dramatically increase weight and surface density.
This high density impedes sound wave movement by reflecting most of the noise. MLVs also reduce structure borne vibration transmission by dampening resonances.
The durable vinyl further resists moisture degradation.
Acoustic Caulk
Specialized acoustic caulks contain flexible polymers and micro-particles designed to shift and move.
When applied at junctions, this flexibility blocks noise leakage through cracks and gaps while also dampening vibration transfer through the Junction by dissipating energy.
Once cured, the durable seal resists deterioration from environmental exposure.
Sound Insulation Products
Materials like Green Glue Noiseproofing Compound leverage vibration damping chemistry combined with composites like Safe and Sound insulation to address both airborne and structure noises.
These integrate seamlessly into existing or new construction through spraying, caulking, and panel installation with reliable long-term performance.
Applications Where Using Sponge For Sound Dampening Is Acceptable
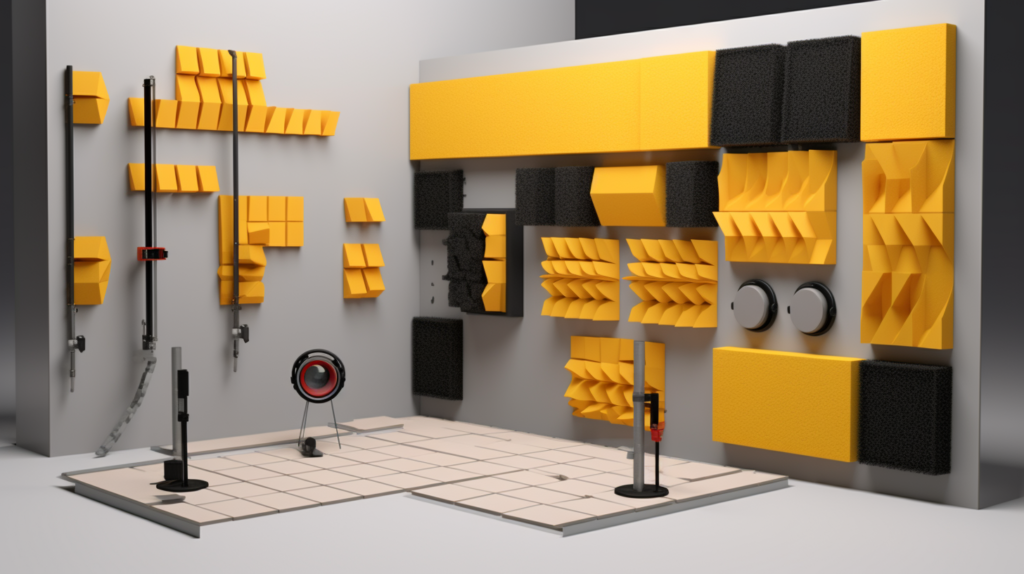
While sponge has definite limitations for effectively soundproofing spaces, the affordable price and easy accessibility supports niche uses for modest sound dampening needs.
Small Acoustic Panels For Reducing Echo
The porous texture of sponge efficiently absorbs higher frequency noises that contribute most to echo generation.
DIY acoustic panels made by covering sponge sheets with decorative fabrics can mount onto walls of smaller rooms like studio bedrooms to dampen reverb and echoes.
Though the effect is limited, it enhances interior ambiance subtly.
Filling Air Gaps Around Outlets
Outlet mounts on walls often leave slight air spaces allowing noise infiltration from adjoining rooms. Inserting small sponge pieces around the outlet edges obtures these openings to prevent noise leakage.
This easy retrofitting forces noise transmission through the dense wall structure rather than bypass leaks.
Temporary Sound Barrier For Equipment
Machinery like generators, pumps and fans required for emergency services often create heavy noise pollution in surrounding regions.
Wrapping sponge sheets around the equipment dampens high pitch mechanical noises appreciably while also absorbing fan vibrations.
This DIY approach creates a makeshift sound barrier minimizing disruption around essential machinery operation.
Portable Acoustic Barriers On Construction Sites
Construction activity generates significant noise from heavy machinery movement and material handling.
While dedicated acoustic wall systems are ideal for longer projects, small construction jobs can benefit from simple portable sponge noise absorbers.
Sponge sheets mounted onto cardboard and plastic frames create movable sound dampening barriers useful for urban sites.
Common Misconceptions Regarding Using Sponge As Soundproofing Material
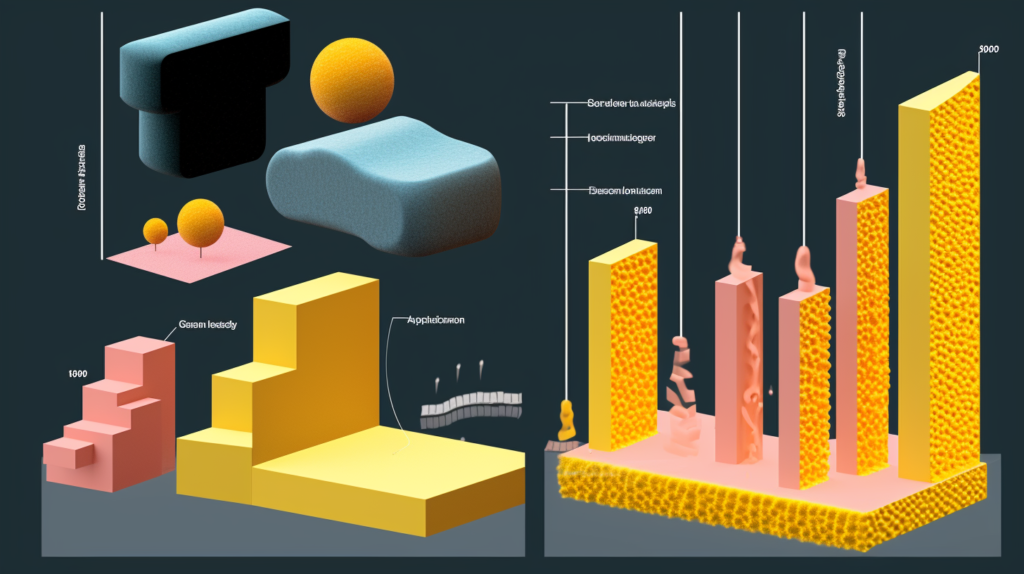
Despite the poor sound blocking capacities, some persistent misconceptions encourage ineffective usage of sponge. Clarifying the factual details on these aspects establishes helpful guidelines.
Sponge Primarily Absorbs Noise Not Blocks It
A common mistake is assuming sponge blocks noise transmission similar to acoustic panels or insulation.
In reality, the porous structure mainly absorbs high pitch airborne noises not lower frequencies.
The absorption has minimal impact on obstruction of impactful noises originating from loud music or machinery penetrating walls. For actual sound blocking, the material itself must impede vibrations.
Sponge Should Not Be The Sole Material Used
While the above niche applications exploit sponge’s sound absorption properties effectively, it performs poorly when used standalone for soundproofing.
Failure to pair with structural caulking, insulating backing or decoupling frames severely limits noise reduction.
Combining sponge with vinyl mass layers and vibration dampeners optimizes overall acoustic performance.
Compressing Sponge Makes It Less Effective
There is also the mistaken assumption that compressing sponge increases density and improves noise blocking. In reality, compression degrades resiliency over time.
The lack of springiness causes diminished contact with surfaces creating gaps that transmit noise. Compressed sponge also shifts easily making stable positioning over long periods difficult.
Conclusion
Sponge lacks the durability, resilience and noise obstruction attributes needed for effective space soundproofing. The key reasons noise abatement professionals oppose relying solely on sponge include:
- Light porous structure allows passage of impactful low frequency noise
- Minimal barrier against vibration transmission including structure borne rumbles
- Long-term loss of compression making stable noise isolation impossible
- Susceptibility to moisture damage causes gradual performance deterioration
- Inability to self-adhere on installation areas unlike purpose-built acoustic materials
The comparable inexpensiveness of sponge does make it suitable for tempering echoes and small airborne sound damping roles.
However, quality acoustic caulking and insulation remains mandatory for permanent noise insulation. Focused application of sponge alongside specialty vinyl barriers and vibration dampeners offers optimal overall sound management.